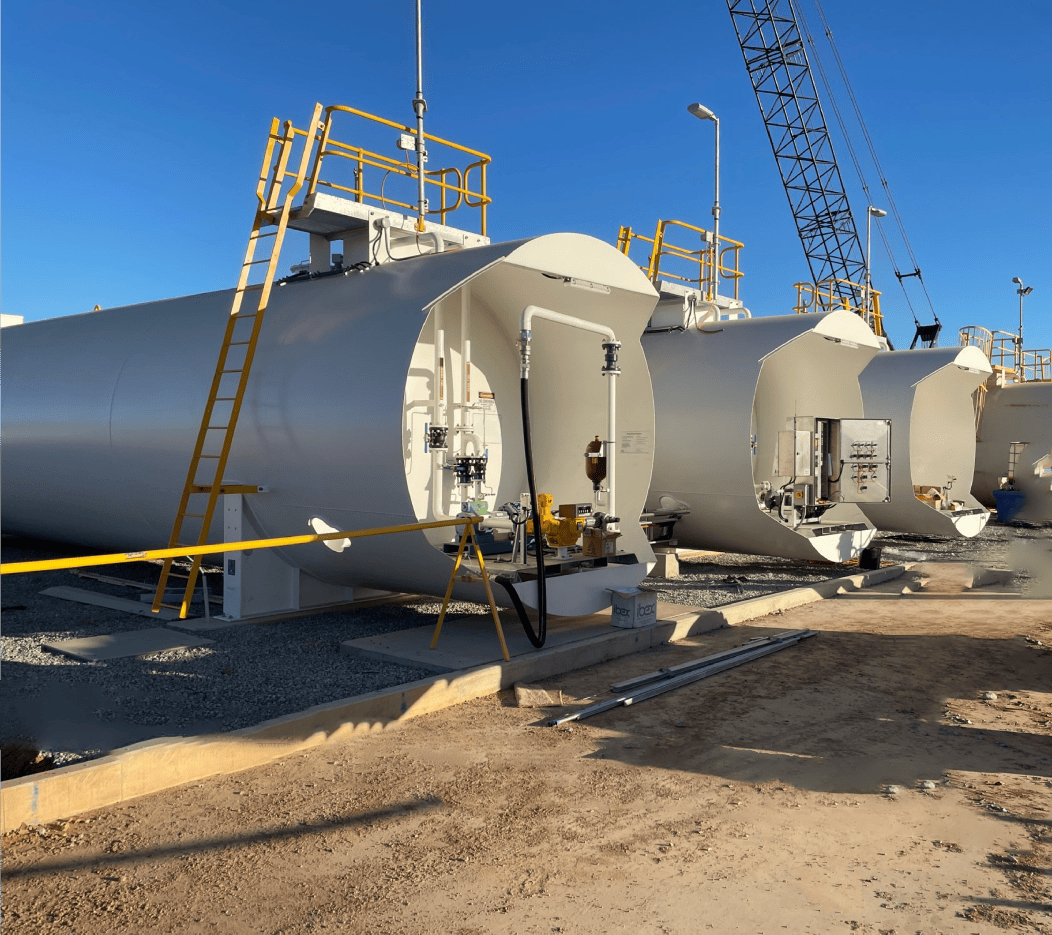
The mining industry is no stranger to the importance of a reliable and efficient fuel supply. With operations often located in remote areas and heavy machinery requiring substantial amounts of fuel, establishing a robust fuel storage facility becomes a crucial aspect of mining operations. While still heavily reliant on fossil fuels to power operations, companies are expected to be more efficient in their use of hydrocarbons and a growing emphasis on ESG (Environmental, Social and Governance) factors continues to reinforce this. The mining sector is looking for tangible strategies to reduce their scope 1 emissions now, whilst maintaining energy reliability and cost efficiency.
The rise of large-scale fuel farms on-site to ensure a secure diesel supply for powering operations.
Traditionally, mining companies have relied on conventional fuel storage methods, such as above-ground tanks or frequent deliveries from external suppliers. However, these methods present numerous challenges, including limited storage capacity, logistical complexities, and increased operational costs. The advent of the bulk fuel farm concept has revolutionised the way mining companies approach fuel storage and management. The introduction of self-bunded tanks with integrated spill containment has played a pivotal role in enabling the rise of these storage options. These tanks simplify and enhance the construction and relocation processes for bulk fuel storage, ensuring safety and efficiency. The dual-wall design of self-bunded tanks prevents leaks and eliminates the need for constructing bunds around tank farms. The flexibility of these fully modular systems enables easy disassembly and relocation of the fuel farm to different sites in response to changing operational needs.
Fuel tank farms enable mining companies to minimise their fuel spend and reduce emissions.
Adopting sustainable energy handling practises is essential for attaining a net-zero future, in addition to storage options. The fuel industry should give priority to actions that will reduce environmental effects over the course of the fuel lifecycle. Businesses can reduce pollution by implementing emissions management and reduction, boosting energy efficiency, and investing in renewable energy. This includes implementing effective fuel transfer systems, using reliable and responsible refuelling and fuel storage solutions, using spill control techniques, and incorporating advanced monitoring technology to make sure environmental regulations have been strictly adhered to. Comprehensive fuel management systems (FMS) deliver consistent and reliable information about fuel consumption and can help businesses implement strategies to improve fuel efficiencies and reduce Scope 1 and 2 emissions. Additionally, encouraging the use of biofuels like biodiesel or renewable diesel can significantly lower greenhouse gas emissions and help create a cleaner, more sustainable energy ecosystem.
A bulk fuel farm serves as a centralised facility designed to store and distribute large volumes of fuel efficiently. These facilities are equipped with robust infrastructure, including specialised storage tanks, advanced fuel monitoring systems, and efficient dispensing mechanisms. By leveraging economies of scale, mining companies can store substantial fuel reserves on-site, reducing their dependence on frequent external deliveries and minimising downtime caused by fuel shortages.
One of the key advantages of a bulk fuel farm is its ability to optimise fuel supply logistics. With dedicated storage capacity, mining companies can strategically procure fuel in bulk during periods of lower prices, ensuring cost savings in the long run. Additionally, streamlined delivery schedules minimise transportation costs and reduce the environmental impact associated with frequent fuel transportation.
The advanced monitoring systems integrated into bulk fuel farms offer real-time visibility into fuel levels, consumption patterns, and potential leaks or spills. This proactive approach enables prompt maintenance and prevents fuel-related disruptions. Understanding where and how fuel is consumed delivers insights on how to optimise fuel deliveries, identify theft, highlight assets issues and minimise equipment downtime.
Mining operations often involve fluctuations in fuel demand due to changing workloads and project phases. The scalable nature of bulk fuel farms allows mining companies to adapt their fuel storage capacity to match these fluctuations, ensuring optimal fuel management and cost-efficiency.
Getting the best of your fuel farm with the Fuelfix Action Methodology.
With growing fuel costs and compliance requirements, organisations are under immense pressure to review their operational processes and improve their fuel and energy infrastructure.
One of the biggest challenges the Australian mine operators face is the lack of accurate and actionable fuel consumption information to facilitate infrastructure and process improvements.
When planning remote fuel storage farms, mining companies must consider consumption rates to determine the appropriate storage capacity. With 16 years of rich history in providing innovative Fuel Management Solutions to the biggest mining companies in Australia, Fuelfix is well placed to assist miners choose the right sized fuel infrastructure in the right location and utilise their fuel management data to optimise fuel usage in terms of costs, maintenance and emissions.
Leveraging data management and our ACTION Methodology, Fuelfix can assist mining companies to meet their energy goals: Reduce fuel costs and emissions, whilst maintaining reliable source of remote power.
Let’s work together on your fuel transition and pave the road for a greener future.
To find out more about how we can help you meet your energy goals, call us at 1300 734 764 or get in touch here.